Our own Tim Cleary and Daniel Bock recently penned an article in Chip Scale Review titled Auto Radar Probe Test Technologies for High-volume Production in which they discussed the needs for today’s onboard integrated circuits and the path to achieving the testing process requirements. The Automotive Electronics Council (AEC) driving test requirements introduced standardized test methodologies for reliable, high-quality components, and ratchets up the need for multi-site calibration and production testing.
Tim and Daniel laid out three pillars to effectively ramping up millimeter-wave radar testing for automotive applications into volume production:
- Multi-site testing. As our authors state:
Once the volume of any chip has reached a certain threshold, there is significant cost pressure to move to testing multiple die in parallel using a multiple device under test (multi-DUT) approach. This approach requires investment in both the tester and the probe card. A half-step in this direction is to put in a switching matrix that keeps the tester resources to a minimum and eliminates the issue of die-to-die crosstalk. It takes longer than true multi-DUT testing, but it does reduce the step time and extend the life of the probe head. Full-on multi-DUT testing first requires a tester with sufficient resources. Several companies now offer this capability. As production-level testing calls for multiple sites with 10+ RF channels, electrical isolation has become a challenge that needs to be considered, particularly when the chip is being tested at the wafer level.
- Multi-site calibration.
The second pillar for production-level test is multi-site calibration. Measurement errors that might be considered insignificant at lower frequencies can become important at millimeter wavelengths. Using a simultaneous multi-site calibration during multi-DUT testing provides the highest electrical accuracy because all the DUT RF channels are in a known and controlled state.
- Automated probe card handling.
The third pillar of production-level testing is automated probe card handling. Changing out the probe card from an RF test cell can be a labor-intensive task requiring a technician to unscrew all the cables connecting the probe card to the tester when a screw-on connector is used. This takes an hour or more and creates the risk of bending the cables in a way that would alter the RF performance or possibly damage the test setup. Implementing a probe station outfitted with blind mate connection capabilities automates the process by moving the stage in or out in the z-direction, mechanically aligning pins so that cables snap together “blindly” and are tightly held in place by pressure. Blind mating allows the RF connection between the probe card and the tester to take place without human intervention. This results in better repeatability and lowers overhead time for setup.
The anticipated future of the autonomous vehicle depends, in part, on the durability of the semiconductors and chips that power radar. We deal with a lot of the new auto-radar devices that are starting to appear and it seems clear that they are all going to be tested to either grade 0 or grade 1 of the AEC-Q100 standard. It’s also clear that this particular niche of the greater auto IC wave is going to be more than a small ripple.
Stay tuned to our blog for more on this subject and read the full text of Tim and Daniel’s article here (PDF): https://www.formfactor.com/wp-content/uploads/Auto-radar-probe-test-FormFactor_v1c.pdf
Click the preview below to download the full article:
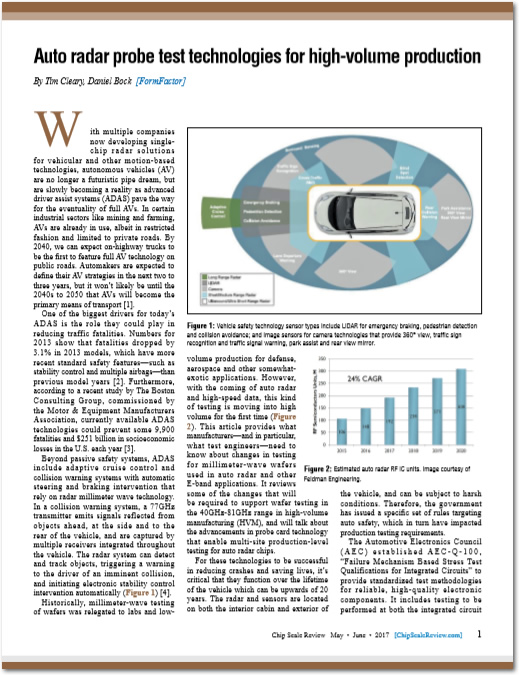